Eastern Redcedar Industry Review Trip
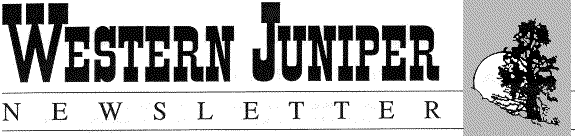
by Scott Leavengood, OSU Extension Service
from the Western Juniper Newsletter, Vol. 1, No. 1, January 1996.
Eastern redcedar (Juniperus virginiana) and western juniper (Juniperus occidentalis) are closely related. Although commonly called a cedar, eastern redcedar is in fact a juniper. On a microscopic level, you cannot tell the two apart.
The U.S. Forest Service sponsored a trip to review the Missouri eastern redcedar industry in 1994. The purpose was to investigate and learn from a 100-year old industry that utilizes a similar species. Information was gathered on wood characteristics, silvicultural practices, harvest practices, transportation systems, log storage, primary and secondary processing, drying , finishing, residue utilization, and marketing.
The eastern redcedar industry review itinerary was arranged and hosted by Shelby Jones, Department of Conservation, State of Missouri. Six Oregon manufacturers actively involved in commercializing western juniper participated in the three-day marathon.
One simple phrase seems to capture the nature of the Missouri eastern redcedar industry: Think Small!
"Small" does not mean the industry is small - hundreds are employed and state-wide impacts are estimated in the millions.
"Think Small" means that equipment used and products produced correspond with physical characteristics of the species. Common log lengths are 46 to 56 inches. In fact, the longest log length seen during the trip was eight feet.
Primary mills visited were two to three-person operations with a circular saw. They manufactured mostly cants for secondary manufacturers. Cants were re-sawed into slats, approximately 3/8-inch thick, which were used in a variety of products, such as drawer and closet lining, wall paneling, and innumerable novelty items (gift boxes, pencil holders, keychains, bird houses, etc.).
Producers have no problems finding markets for their residual material, such as sawdust, slabs, and edgings. One primary manufacturer with three employees commented that income from residual material brought in $30,000 a year.
Slabs and edgings are usually shaved in planer mills and sold for small animal bedding, after air-drying for several months. Some mills have their residual material ground with a tub grinder, which is then sold for mulch. One large manufacturer uses their residual to make particle board for drawer and closet lining. You never see big sawdust piles or other residual at cedar sawmills, compared to oak mills which have real problems disposing of their waste material.
For More Information Contact: Scott Leavengood, OSU Extension Service (541-883-7131)
For more information on eastern redcedar, see the on-line Annotated Bibliography of Eastern Redcedar