Newsletter: The Human Dimension
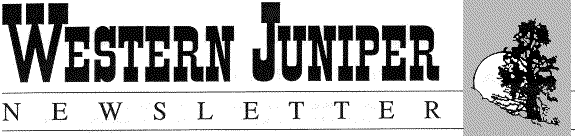
The Human Dimension in the World of Western Juniper: There Was This Guy in Prineville...
by Larry Swan, USDA Forest Service, Winema National Forest
from the Western Juniper Newsletter, Vol. 1, No. 2, Summer 1996.
It is rare to talk to anyone about western juniper without Gary Gumpert's name coming up(1). Gary had a mill in Prineville from the mid- to the late-1970s. During the time he ran the mill, he probably produced and sold more solid-wood juniper product than anyone ever did before him or has since. The mill was sold in the late-1970s and burnt down soon thereafter.
Following is a brief description of Gary's operations, equipment, and products:
At the time the mill was sold, Gary said he was processing about two-thirds incense cedar and one-third juniper. He employed six to seven people steadily, and up to 12 occasionally.
Gary did most of his own logging (90%). He cut 24- to 32-foot juniper logs and transported them to the mill. A major selection criteria for juniper saw logs was limbiness - the fewer the better. He did not necessarily want large logs because they were often rotten in the center. According to Gary, most of the costs involved with juniper happen before the log gets to the mill. Gary said he never did figure-out an economical way to harvest juniper.
The head rig in Gary's sawmill was a 54-in. band saw with a .105-in. kerf and taper blocks. He said he spent alot of time working-out best tooth and gullet angles, depths, and spacing. Gary used a "real spendy" 32-in. circular saw with the same kerf as the head rig for resaw. The resaw had close to 300 teeth, and required lots of water and close attention to tension.
For secondary processing, Gary had two moulders with a saw in the middle for making tongue-and-groove (T/G) paneling. He also built himself a machine to make end-match paneling. Lumber was finished with a large drum sander using 120 grit paper.
Sawing and logging operations were usually not conducted simultaneously. Gary said they tended to saw, finish, then restock. Much of the sawing was done in the winter. He preferred working with green logs, but on occasion would use logs up to one-year old, depending on how they had been stored. Standard log-length was eight-feet and target size board was one-inch by six-inches. This was then resawn to 7/16-in. It usually took 16 to 20 eight-foot logs to make about a 1,000 bd. ft. of lumber.
Gary said juniper was harder to cut than incense cedar. "Burley growth" patterns caused the headrig to "snake", but proper saw sharpening, RPMs, and sufficient water solved 80% of the problem. Juniper logs also required more passes with the head rig to square them up, and often had to be turned four and five times on the saw carriage to minimize sap/heartwood mixtures in the same board.
Up to 40-50% of a log went into the hog bin, according to Gary. Overall, he guessed that 50-60% might be lost during primary breakdown and another 30-40% during secondary processing. Gary thought you would be lucky to get 40% yield out of a juniper log.
Gary made his own small kiln. He air-dried lumber before putting it in the kiln and, if it was not too hot, oriented lumber stacks while air-drying to catch the prevailing breeze. Seven to nine stickers were used per eight-foot board, with the outside stickers at each end. He protected lumber from the sun to prevent yellowing. Moisture content was usually 20-30% before being put into the kiln. More lumber was dried in the spring and fall, when it was not so hot.
Kiln schedules probably did not exceed 130-140 degrees F normally, and recycled moisture was sprayed back into the kiln. Target moisture content was 10-12%. If logs had been laying around for awhile, kiln temperatures were raised to 150 degrees F to kill "bugs".
Gary said they made a lot of different products. The "main-stay" turned-out to be decorative paneling, which was T/G, end-matched, and generally three to five inches in width, random length. His main customer was Simpson Lumber. He sold it by the box, 32 sq. ft. per box. Wholesale price was $18/box for juniper and $15/box for incense cedar.
Other juniper products included: Tables, chairs, gun cabinets, display panels, coffee table slabs, and fireplace mantle slabs. Slabs were stored under the mill for several months, where it was cool and dry, to season them.
Gary also did some laminating. He would take half-inch thick by about two-inch wide cull boards, put enough of them together to make four- to six-inch wide blocks, and then would re-saw the blocks to make countertops and other products.
Gary now owns a farm/ranch operation outside of Prineville, as well as a trucking business. His juniper products are still owned with pride by many people, and if the word "juniper" is brought up in a conversation, you often hear them say: "There was this guy in Prineville..."
1. This article is based on notes from a telephone conversation Larry Swan had with Gary Gumpert, February 1, 1995. Larry accepts all blame and responsibility for any errors or omissions, and thanks Gary for his patience and time.