Western Juniper Debarking Project
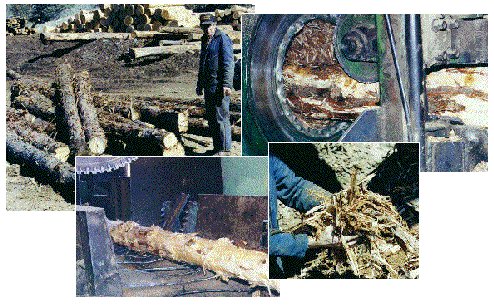
Western Juniper Debarking Project
Scott Leavengood, Oregon State University
Larry Swan, USDA Forest Service
Bill Breedlove, Western Juniper Industry Facilitator
Abstract
A number of characteristics including rot, bark seams, spiral grain, large and numerous limbs, and rapid taper, render the vast majority of western juniper logs unsuitable for sawing into lumber. Therefore, to be utilized efficiently, markets must be developed for juniper fiber products, such as medium-density fiberboard or hardboard. The manufacturing processes for many fiber products require "clean chips", that is, chips containing a very low percentage of bark and debris. To achieve low levels of bark in a chipping operation, the logs must be debarked prior to chipping. Experience with incense-cedar and other species with fibrous or "stringy" bark has caused manufacturers to be concerned about juniper bark plugging debarking and waste handling equipment, wrapping around cutterheads, or otherwise causing debarking difficulties. Ring debarkers, a rosserhead debarker, and a chain flail delimber were tested in this project. The rosserhead debarker appeared to debark most effectively (greatest percentage of bark removed) however the particular piece of equipment used was very slow. The ring debarkers performed adequately however some minor equipment plugging occurred in one instance due to the fibrous nature of western juniper bark. The chain flail delimber also performed satisfactorily, although delimbing "quality" will have to be high (limbs trimmed flush to the bole) for this machine to perform well. For smaller-scale western juniper manufacturers, a small high-speed rosserhead (approximate cost $x used, $x new) may be the most effective method for bark removal.
Purpose
The purpose of this project was to test different western juniper debarking methods for effectiveness. Results will give entrepreneurs guidance for methods to effectively produce "clean" chips and thereby maximize utilization of juniper fiber.
Need
The vast majority (approximately 80-90 percent) of juniper logs that will be harvested are unsuitable as sawlogs. Therefore, in order to effectively utilize western juniper, markets for fiber products such as medium-density fiberboard and hardboard must be explored. The manufacturing processes for these products generally require "clean" chips, that is, chips that contain a very low percentage of bark and debris. The most effective way to obtain clean chips is to debark the logs. The stringy and fibrous character of western juniper bark has caused some concern among manufacturers for fears of equipment plugging and the potential for fires starting in bark grinding ("hogging") equipment. A method is needed to debark juniper that is efficient, cost-effective, and suited to the stem form of juniper (often highly tapered with large limbs and bark seams).
Background
About five years ago, the Winema National Forest, located in south-central Oregon, organized a "focus group" of small, medium, and large wood product manufacturers. The purpose was to identify critical issues from a manufacturer's perspective, potential areas of cooperation, and who would consider working together with the Forest Service, and other government and nonprofit economic development organizations. Impetus to discussions was provided by the shutdown of several local mills: Over the course of just 18 months, 1,200 manufacturing jobs were lost out of a total regional manufacturing employment base of less than 4,000. The "focus group" met informally three times and, as might be suspected, identified "supply" as the major issue facing the industry.The focus group expressed an interest in better utilization of and markets for western juniper (Juniperus occidentalis). While it is highly unlikely that juniper will be the "salvation" of the Northwest timber industry, there is real potential for the creation and retention of jobs in harvesting, transporting, manufacturing, and marketing western juniper. Projects such as this one are designed to help manufacturers overcome production challenges so that they may effectively utilize western juniper.
Prior Work
There is no known prior work to determine the effects of different debarking techniques for western juniper. Species with similar bark such as incense-cedar, western redcedar, and redwood are often debarked with rosserhead debarkers. While these machines are often slower than ring debarkers and more sensitive to operator skill-levels, they do work quite well on species with stringy or fibrous bark. Some manufacturers in the redwood and western redcedar industry have used hydraulic debarkers (debarking using high-pressure water spray). The use of hydraulic debarking equipment has declined in recent years with the increasing concerns for water quality. The eastern redcedar (another species with very similar bark) producers visited by members in the western juniper commercialization project in 1994 and 1995 did not use debarking equipment.
Current Practices
Many western juniper manufacturers currently do not use debarking equipment. The manufacturers have expressed a need for debarking equipment, however many are unable to afford or justify the larger scale ring debarkers (approximate cost?) used by many sawmills. In addition, there is a fear that the ring debarkers will not effectively remove the bark from western juniper. Equipment that is lower cost, smaller scale, effective for juniper bark, and relatively high-speed is needed. One juniper sawmill has recently purchased a high speed rosserhead debarker based in part on the results of this project. This mill had been chipping juniper without debarking and their customers had begun to request cleaner chips.
Methodology
On January 27, 1995, fifty western juniper logs from Lake County, Oregon, were debarked at Modoc Lumber in Klamath Falls, Oregon. Logs were 26-30 feet in length with a minimum small end diameter of 6 inches. Logs were of generally "poor quality", with rapid taper, large and numerous knots, and numerous bark seams. Three types of debarking equipment were used: a small and a large ring debarker, and a 1960's vintage rosserhead debarker. Modoc Lumber used the rosserhead debarker primarily for logs too large to be debarked by the large ring debarker. With the decline in diameter of raw material being harvested in recent years, the rosserhead was rarely used.The logs were then sawn into lumber, although the primary target for the project was chips for Weyerhaeuser Hardboard in Klamath Falls. Weyerhaeuser had been buying juniper chips and were asking their suppliers to provide cleaner chips.
On March 25, 1996, another juniper debarking trial was conducted at Klamath Veneer in Klamath Falls, Oregon. Logs averaged 80-90 years old, 26 feet in length and 14-18 inches in diameter. All logs were harvested from a mixed conifer stand in northeast California. Knots were approximately 2-3 inches in diameter and spaced 6-12 inches apart. These logs were described as "better than average" quality with less butt rot and bark seams than normal. Klamath Veneer utilizes a Salem ring debarker that can process logs up to 27 inches in diameter. The debarker had 5 cutting arms reported to be in good condition by Dave Machado, mill manager.
On October 21, 1996, 10-12 juniper logs were debarked by Circle DE Lumber using a stand-alone Peterson Pacific, Model 4800 chain flail delimber. All logs were green.
Results
No significant difficulties were encountered at Modoc Lumber with any of the 3 types of debarking equipment. Many spectators present during the debarking trials expressed surprise that the logs debarked as well as they did. Some spectators mentioned the possibility that many of the logs may have been frozen and therefore the bark broke off in "chunks" vs. being peeled off in long strands.Operators of both the large and small ring debarkers ran their machines slightly slower than they ordinarily would with pine or fir. However, both operators mentioned that they were taking more time due to having an audience as well as working with a new and unfamiliar species. The ring debarkers both produced very long (6-8 inches) "slivers" of bark and wood. For many purposes, such as bedding or mulch, this material would require further processing. Weyerhaeuser Hardboard in Klamath Falls analyzed the bark and found it to be approximately 70 percent bark and 30 percent wood.
The rosserhead debarker appeared to remove bark most effectively, however the trade-off was in time; each log required approximately 5 minutes. The bark from this machine was ground very fine, and would likely not require further processing to be sold as mulch or bedding. Bark vs. wood content was nearly identical for the material produced by the rosserhead debarker as for the ring debarkers (70:30).
The chips from Modoc Lumber were analyzed for bark content by Weyerhaeuser Hardboard in Klamath Falls. Bark content was 2-3 percent, reported by Weyerhaeuser to be an acceptable level for their hardboard plant. In the past, bark content had been 6.5-7.5 percent for chips produced from logs with bark (whole log chipping).
Minor difficulties were experienced during the ring-debarker trial at Klamath Veneer. The operator had to stop the machine occasionally to unplug and untangle long strips of bark from the cutterheads. Logs were bucked to 8 feet in length which also presented some challenges to effectively hold the logs securely during debarking. The operator mentioned that 9 feet and longer log lengths would be preferred. Debarking time was similar to white fir, ponderosa pine and lodgepole pine. The operator stated that the logs debarked in strips like incense-cedar, though not as thick. The material was long enough that it would plug the waste handling equipment and therefore equipment modification would be required. The operator commented that the logs were debarking well and from experience, guessed that were the logs chipped, the chips would contain 3 percent bark or less. Wood loss was not excessive.
No significant challenges occurred during the chain flail debarking trial. The operator commented that improved delimbing quality (limbs trimmed flush to the bole) would be required and estimated if the logs were chipped, the chips would contain approximately 2 percent bark.