Western Juniper Log Storage Project
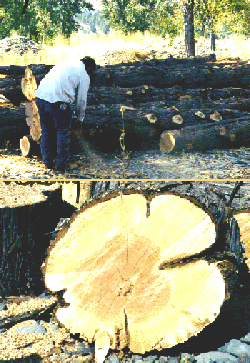
Western Juniper Log Storage Project
Scott Leavengood, Oregon State University
Larry Swan, USDA Forest Service
Bill Breedlove, Western Juniper Industry Facilitator
Abstract
Initial product trials in the western juniper commercialization project revealed a potential problem of excessive splitting and checking during drying and remanufacture. It was theorized that the problem may be due to "raw material handling", e.g., excessive storage time or lack of end-coating. Splitting reduces raw material recovery and may cause reductions in quality and value of finished products. Therefore, the Western Juniper Log Storage project was conducted to study the effects of differing log storage methods (end-coated vs. non end-coated) and storage duration on product recovery and value. Juniper logs were harvested and a portion of the logs were end-coated immediately after felling while the remaining logs were left uncoated. Some of the logs were sawn into lumber, dried, and remanufactured into finger-joint blanks after being stored for 30 days, and the remaining logs were processed after 250 days of storage. Recovery figures for lumber and finger-joint blanks were calculated for both storage periods. Lumber recovery values were approximately 1.66 (i.e., the lumber recovered was 1.66 times the volume predicted by the gross log scale) for logs stored 30 days. Lumber recovery for logs stored 250 days was approximately 1.27. In this project, lumber recovery was approximately 40 percent greater for logs stored for 30 days than for logs stored for 250 days. Finished product recovery3 in the form of finger-joint blanks did not appear to be significantly affected by duration of log storage.
Purpose
The purpose of this project was to compare results of different western juniper log storage methods and storage duration on product recovery and value. Results will give entrepreneurs guidance for methods to improve product recovery and value.
Need
Initial product trials with western juniper indicated a potential problem with end-splitting. Observers commented on the tendency for small end-splits in green lumber to continue propagating (in some instances up to twelve inches or more) during remanufacturing and while the wood was in service. End-splitting is not an unusual problem for wood. It does seem, however, that western juniper may split more easily and to a greater extent than other commonly used species. What is needed is to determine if the extent of splitting in juniper is in fact a rarity, or if "material handling" may be a significant factor in the problem. A separate project has been conducted to study drying techniques for western juniper to improve finished product quality.
Background
About five years ago, the Winema National Forest, located in south-central Oregon, organized a "focus group" of small, medium, and large wood product manufacturers. The purpose was to identify critical issues from a manufacturer's perspective, potential areas of cooperation, and who would consider working together with the Forest Service, and other government and nonprofit economic development organizations. Impetus to discussions was provided by the shutdown of several local mills: Over the course of just 18 months, 1,200 manufacturing jobs were lost out of a total regional manufacturing employment base of less than 4,000. The "focus group" met informally three times and, as might be suspected, identified "supply" as the major issue facing the industry.The focus group expressed an interest in better utilization of and markets for western juniper (Juniperus occidentalis). While it is highly unlikely that juniper will be the "salvation" of the Northwest timber industry, there is real potential for the creation and retention of jobs in harvesting, transporting, manufacturing, and marketing western juniper. Projects such as this one are designed to help manufacturers overcome production challenges so that they may effectively utilize western juniper.
Prior Work
There is no known prior work to determine the effects of log storage method and storage duration on recovery and value of western juniper products. Work has been done on storage methods for other species, however. Many researchers have reported the benefits of water spray or water storage to reduce staining due to fungi and end-checking. It is unlikely that western juniper manufacturers will use water spray or storage techniques due to high capital costs in equipment and maintenance as well as increasing environmental restrictions. Therefore, water spray or storage was not investigated in this project. End-coating, on the other hand, requires far less capital outlay and therefore is more practical for most juniper manufacturers. End-coating has been shown by many researchers to reduce degrade in logs during storage providing the coatings are applied when the logs are still very green (Rosen and Miceli, Rice). Duration of storage has been studied (generally in conjunction with water spray or storage) and has been shown to effect product recovery. Carpenter and Toole (1963) found that after one year of storage without water spray or end-coating, checking and staining were so severe in eastern cottonwood (a species with very low resistance to staining and decay) that the logs were "...not worth sawing".
Current Practices
Rot, bark seams, spiral grain, large and numerous limbs, rapid taper, and other factors render the vast majority (approximately 80-90 percent) of western juniper logs unsuitable for sawing into lumber. Due to poor log "quality", it often takes several months to accumulate sufficient quantities of sawlogs to economically operate a mill. Juniper, like other wood species, develops end checks rapidly after harvesting and long storage periods aggravate the problem. End-coating helps to retard moisture loss, and therefore reduces checking and splitting. However costs involved with end-coating in both labor and material result in the practice being used primarily for higher value species. Many manufacturers working with juniper currently store logs for very long periods before processing and do not use end-coat.
Methodology
Logs for the study were harvested near Dairy, in southcentral Oregon in early October of 1995 by High Desert Wood Products. All logs were harvested from the same stand of trees and were bucked to twenty-six feet in length. Diameter at breast height varied from approximately eight to fourteen inches. The logs arrived at the mill on October 17th, 1995. The logs were decked on a south-facing slope and were oriented with the prevailing wind toward the butt ends of the logs. The following day, of the logs were end-coated by Bill Breedlove, Western Juniper Industry Facilitator.
Phase I:
On November 4, 1995, approximately thirty days after harvesting, six logs were bucked into segments 8Ω feet in length, resulting in a total of eighteen segments. The average small and large end diameters for the segments were eleven and fifteen inches.
On November 8th and 9th, the eighteen segments were sawn into primarily 4/4 thick x 3 inch wide x 8Ω feet long lumber at All Native Hardwoods in Roseburg, Oregon. Lumber recovery was recorded for each log segment. The lumber was covered and shipped to Oregon State University's Forest Products Department for drying. After drying, the material was shipped to Henderson Millworks in Klamath Falls, Oregon to be remanufactured into finger-joint blanks. The target width for ripping was 2æ inches, however two "back-up rips" of 2Ω and 2 inches were allowed. Material was graded as clear or tight-knot and tallied.
Phase II:
On June 19, 1996, approximately 250 days after harvesting, the remaining logs were bucked into thirty-five segments, 8Ω feet in length. The average small and large end diameters for the segments were ten and fourteen inches. On June 20 and 21, the logs were sawn at All Native Hardwoods in Roseburg to the same size specifications as in the first phase of the project. Lumber recovery was again recorded for each log segment. Material was dried in OSU's steam kiln and then delivered to Rainier Wood Products in Sweet Home, Oregon, to be remanufactured into finger-joint blanks. The target rip width was 3 inches and allowed only one "back-up rip" width of 2 inches. As in Phase I, the material was graded as clear or tight-knot and tallied.
Results
Gross log scale for the log segments in Phase I (logs stored approximately thirty days) was 780 board feet using Scribner Decimal C tables. Total volume recovered in 4/4 x 3 x 8Ω lumber was 1297 board feet. Therefore total lumber recovery1 was 1.66 (i.e., the lumber recovered was 1.66 times the volume predicted by the gross log scale).
For the remanufacturing portion of Phase I, recovery was calculated as a percentage of lumber input (BF finger-joint blanks ˜ BF lumber). Of the 1200 board feet of lumber sent to be remanufactured (97 board feet were provided to interested parties for small product samples) 641 board feet or 53.4 percent were recovered as finger-joint blanks. The recovery breakdown by grade was as follows:
- clear 2æ" x RL- 321 BF
- tight-knot 2æ" x RL- 222 BF
- tight-knot 2Ω" x RL- 38 BF
- tight-knot 2" x RL- 24 BF
(36 board feet were removed before tallying and used for product trials)
Gross log scale for the log segments in Phase II (logs stored approximately 250 days) was 1285 board feet using Scribner Decimal C tables. Total volume recovered in 4/4 x 3 x 8Ω lumber was 1636 board feet and therefore recovery was 1.27.
For the remanufacturing portion of Phase II, 1636 board feet of lumber were sent to be remanufactured and 823 board feet (50.3 percent) were recovered as finger-joint blanks. The recovery breakdown by grade was as follows:
- clear 3" x RL- 306 BF
- clear 2" x RL- 104 BF
- tight-knot 3" x RL- 378 BF
- tight-knot 2" x RL- 35 BF
Discussion
In this project, total lumber recovery (as a percentage of gross log scale) decreased nearly 40 percent for logs stored for 250 days vs. logs stored only 30 days. Those with experience sawing western juniper know that this amount of variability might be explained due to raw material "quality" (degree of taper, amount of rot present, log size, degree of bark fluting, spiral grain, etc.) alone and therefore duration of storage may not be a factor at all. Some steps were taken to avoid this problem. All logs were harvested from the same stand of trees. This was done intentionally to attempt to minimize variability between logs. In addition, the average log diameters were very similar for both phases of the project. Analysis of the recovery data revealed that, as expected, there was a great deal of variability in recovery between individual logs. Figure 1 shows the range of variability in lumber recovery (as represented by the range in "height" of the boxes) for both phases of the project. The horizontal bar across the boxes is the average lumber recovery and the vertical "tails" reflect the high and low extremes of the data. Statistical analysis of lumber recovery data provided evidence of a difference in recovery between the two phases of the project above and beyond what can be explained due to inherent variability in log quality.Total finished product recovery (as a percentage of lumber tally) was approximately 53.4 percent and 50 percent for logs stored 30 days and 250 days, respectively. This small amount of variability is likely insignificant. Therefore it appears that while lumber recovery is adversely affected by long storage periods, finished product recovery is not.
Value recovery, as evidenced by grade recovery of finger-joint blanks, was very similar for the two phases: 26.8 percent clear material (as a percentage of lumber input) was recovered in Phase I and 25.1 percent clear material was recovered in Phase II. Because the material was remanufactured at different companies given different instructions (two backup rips in Phase I and one backup rip in Phase II), it is difficult to determine if duration of storage impacted value recovery.
During the project, the ability was lost to distinguish end-coated vs. uncoated logs2. Therefore, unfortunately, it is impossible to determine the effect of end-coating on product recovery from this project. Based on end-coating studies for other wood species, it is highly probable that the decline in lumber recovery witnessed in this project was due, at least in part, to end-checking on the uncoated logs.
Recommendations
As with other species, the use of as short a storage period as is practical is recommended to obtain optimal western juniper lumber recovery. While this project was unable to demonstrate the recovery benefits of end-coating, studies with other species have demonstrated such benefits. To maximize volume and value recovery, juniper logs should be end-coated immediately following felling.
Literature Cited
Carpenter, B.E. and E.R. Toole. 1963. Sprinkling with Water Helps Protect Hardwood Logs in Storage. Southern Lumberman, 207(2576):25-26.Dry Kiln Operator's Manual- Ag. Handbook No. 188. Revised 1991. USDA Forest Service- Forest Products Laboratory, Madison, Wisconsin. 274 pp.
Rice, R.W. 1995. Transport Coefficients for Six Log and Lumber End Coatings. Forest Products Journal, 45(5):64-68.
Rosen, H.N. and C.M. Miceli. 1980. End Coating Effects on High-Temperature-Dried Yellow-Poplar. Forest Products Journal. 30(4):47-50.
